Palisades Wildfire and Its Impact on Supply Chains and Logistics
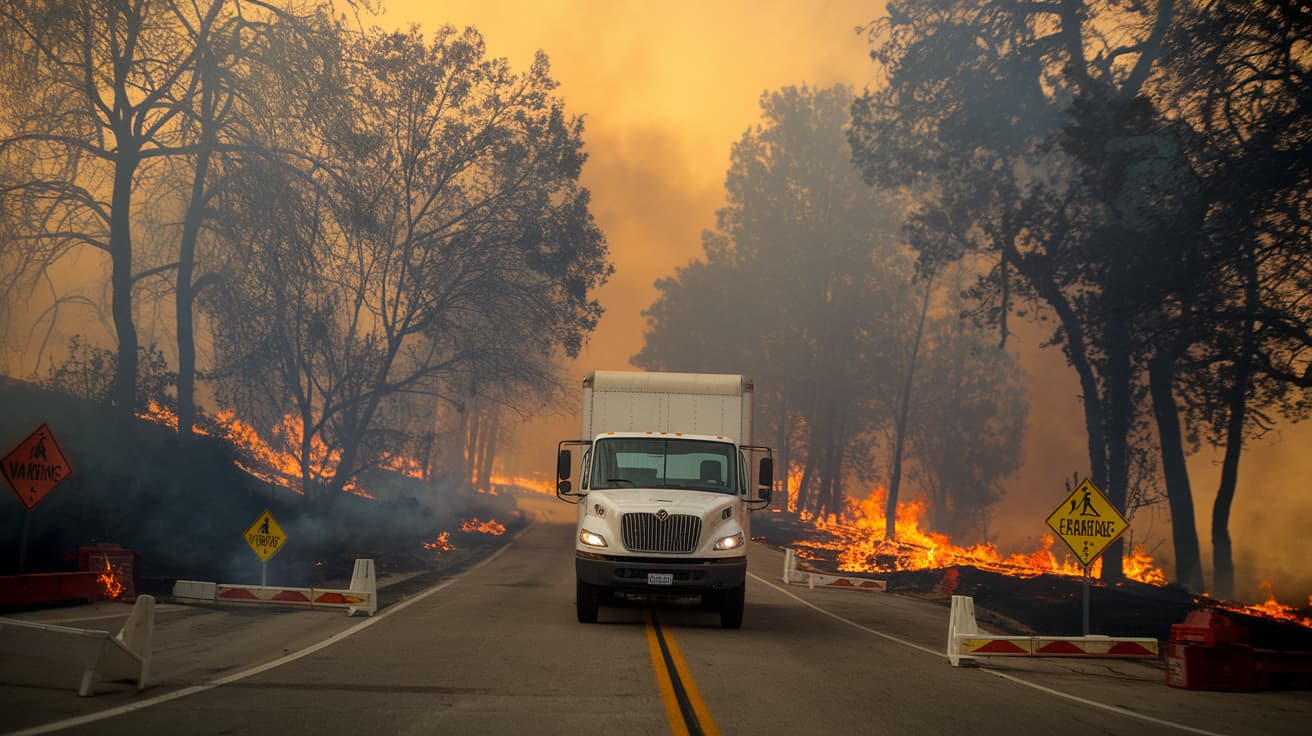
In January 2025, the Palisades wildfire burned for six days, destroying over 300 buildings and damaging 13,300 more in Santa Monica and Malibu. The fire displaced families, disrupted daily life, and caused heavy losses for businesses relying on key infrastructure. The Palisades fire alone is estimated to have disrupted supply chains worth millions of dollars, as highways were closed, warehouses evacuated, and logistics networks paralyzed. For an industry already stretched thin by increasing consumer demands, the stakes have never been higher.
While the event has brought devastation, it also calls attention to a pressing question: how can businesses prepare for the economic and operational shocks that wildfires bring? In this article, we’ll explore the specific challenges this disaster posed for logistics and outline proactive measures to mitigate similar risks in the future.
The Growing Threat of Wildfires
The Palisades Fire ignited on January 7, 2025, in the Pacific Palisades neighborhood of Los Angeles, California. This affluent coastal area, nestled between the Santa Monica Mountains and the Pacific Ocean, is renowned for its scenic beauty and as a residence for numerous Hollywood celebrities.
The wildfire rapidly spread due to strong Santa Ana winds, consuming over 23,000 acres and destroying more than 5,300 structures. The flames advanced through rugged terrains and residential zones, leading to widespread evacuations and significant property loss.
As of January 12, 2025, containment efforts have achieved approximately 13% control over the fire. However, the situation remains critical, with thousands of residents displaced and emergency services working tirelessly to manage the ongoing threat. Overall, the economic cost of these fires is projected to exceed $20 billion, with significant impacts on supply chains. Businesses are facing higher costs, delayed shipments, and reduced customer satisfaction.
Why Wildfires Are a Concern for Logistics
Wildfires disrupt logistics by damaging infrastructure, such as roads and warehouses. They also create labor shortages as workers evacuate affected areas. Smoke and poor air quality further slow down operations, forcing businesses to find alternative solutions.
For example, the closure of Interstate 5 during peak wildfire activity delayed shipments to Southern California by up to 48 hours, causing significant losses for many businesses.
Case Study: The August Complex Wildfires of 2020
Key Impacts on Logistics
The August Complex wildfires burned over 1 million acres in Northern California, making it the largest wildfire event in the state’s history. It disrupted critical supply routes, including U.S. Highway 101, and damaged several warehouses in the Mendocino area.
The economic impact was severe, with transportation costs increasing by 25%. Businesses had to reroute shipments, resulting in delays and increased fuel expenses. Some smaller logistics firms went out of business due to the prolonged disruptions.
Lessons Learned
The August Complex fires highlighted the importance of diversifying transport methods and investing in resilient infrastructure. Businesses that relied on AI-driven logistics tools were better equipped to adapt, as these tools helped identify alternative routes and optimize operations during the crisis.
Additionally, companies with decentralized warehouse systems faced fewer challenges, as they could shift inventory to unaffected locations.
Current Wildfires: Logistics Disruptions in 2025
Transportation Challenges
In 2025, wildfires have led to the closure of key highways, including Interstate 80 and portions of Highway 101. These closures have forced logistics companies to rely on longer, less efficient routes, increasing delivery times and fuel costs.
Furthermore, rail services in Northern California have been disrupted due to fire damage to tracks and surrounding areas, affecting the transportation of bulk goods like grain and building materials.
Impact on Warehousing
Several warehouses in affected regions have been evacuated or shut down due to fire risks. Some facilities have suffered significant damage, leading to the loss of inventory. Businesses relying on these warehouses are struggling to meet customer demands.
In addition, poor air quality has slowed down operations in nearby warehouses, as workers are unable to perform tasks efficiently in hazardous conditions.
Mitigating Risks: Solutions for Businesses
1. Diversify Transport Methods
To minimize disruptions, businesses should diversify their transportation methods. Combining road, rail, and sea transport can reduce reliance on a single mode and provide alternatives during emergencies.
For example, using rail transport for non-urgent goods can free up road resources for critical shipments, ensuring timely deliveries even during crisis situations.
2. Leverage Technology
AI and real-time tracking systems can help businesses adapt to dynamic situations. These tools enable companies to reroute shipments, optimize fuel usage, and predict disruptions before they occur.
For instance, companies using AI-driven logistics software during the August Complex fires were able to reduce delivery delays by 30% compared to those relying on manual planning.
Preparing for Future Challenges
Wildfires are an unavoidable challenge for businesses operating in vulnerable regions. By learning from past events like the August Complex wildfires and implementing proactive measures, companies can minimize disruptions and build more resilient supply chains.
Preparing for natural disasters is not just about managing risks—it’s about ensuring that businesses can continue to serve customers and thrive, even in the most challenging circumstances.