Six Sigma and How It Helps SMEs Avoid Costly Technology Mistakes
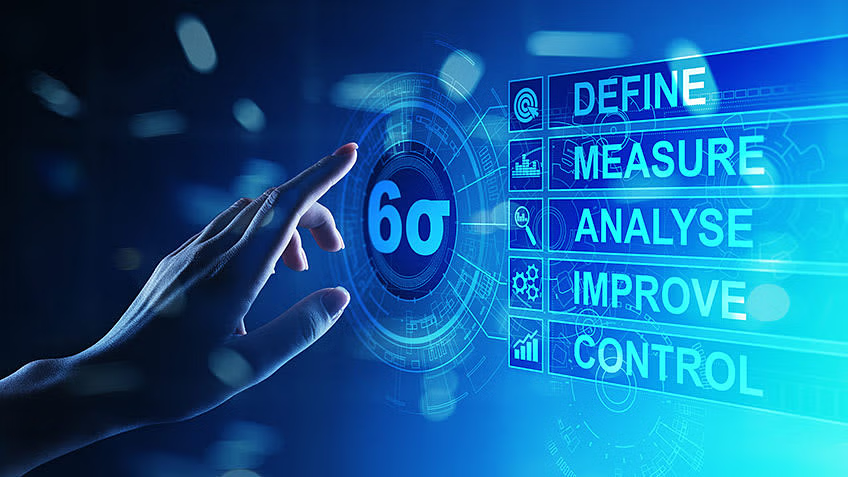
In an era where efficiency and precision determine business success, Six Sigma has emerged as a leading methodology for process optimization. Originally developed for manufacturing, Six Sigma is now widely applied across industries, including technology, logistics, and software development. By minimizing defects and maximizing efficiency, businesses can reduce costs, improve customer satisfaction, and scale effectively.
For SMEs and growing enterprises, integrating Six Sigma principles can help avoid costly technology and operational mistakes. This guide explores how Six Sigma works, why it matters for business growth, and how it can be applied to digital transformation, AI, and business scaling.
Table of Contents
2. The Role of Six Sigma in Business Efficiency
3. Why SMEs Need Six Sigma to Scale Effectively
4. Applying Six Sigma in the Digital Age
5. Real-World Application: How Six Sigma Can Improve Your Business
6. Conclusion: Should Your Business Adopt Six Sigma?
What is Six Sigma?
Six Sigma is a method that helps businesses reduce errors, improve quality, and increase efficiency. It focuses on analyzing processes and removing waste to improve performance. This method is widely used in manufacturing, technology, and logistics.
Six Sigma follows two main frameworks:
|
Originally developed by Motorola, this approach is now used by major companies like Amazon, IBM, and General Electric.
The Role of Six Sigma in Business Efficiency
Businesses today must operate efficiently to stay competitive. Errors, delays, and waste can lead to financial losses and customer dissatisfaction. Six Sigma provides a structured way to analyze problems, find solutions, and make operations more efficient. By focusing on data, companies can eliminate mistakes and create smoother workflows.
Reducing Errors and Improving Quality
Errors in business processes can slow down operations and increase costs. Whether it’s in manufacturing, logistics, or software development, defects must be minimized. Six Sigma helps businesses identify weak points in their processes and create solutions that prevent mistakes before they happen.
Companies that use Six Sigma see higher product quality and lower waste levels. By following structured problem-solving techniques, businesses ensure that every step in their process meets high standards. This reduces the risk of failures and improves overall efficiency.
Boosting Productivity and Cost Savings
Every business wants to produce more while spending less. Six Sigma helps teams streamline operations and remove unnecessary steps. By improving workflow efficiency, companies can handle more work without increasing labor or operational costs.
For example, a company using Six Sigma may find that automating certain tasks leads to faster results. Reducing waste and unnecessary delays allows businesses to save money, meet deadlines, and focus on growth.
Using Data for Smarter Decision-Making
Many businesses make decisions based on guesswork, which can lead to costly mistakes. Six Sigma focuses on data-driven decision-making, ensuring that choices are based on facts and measurable results. Companies use statistical tools to track performance and find areas for improvement.
By using real-time data, businesses can quickly adjust to market changes, customer needs, and new technology trends. This method ensures that companies stay competitive and improve continuously.
One growing trend is combining Six Sigma with AI and digital transformation. AI improves automation, while Six Sigma ensures accuracy and efficiency.
|| Read more: Integrating AI into Business Strategies – Preparing for 2025
Why SMEs Need Six Sigma to Scale Effectively
Small and medium-sized enterprises (SMEs) face many challenges when expanding. These include operational inefficiencies, lack of structured processes, and difficulty maintaining quality. Without proper management, these problems slow down growth and increase costs.
Six Sigma helps SMEs identify weak points and improve efficiency. It allows businesses to scale without sacrificing quality. By focusing on data and structured improvement methods, SMEs can reduce waste, improve productivity, and enhance customer satisfaction.
Solving Common Growth Challenges
When businesses expand, they often experience growing pains. More orders mean more inventory, more customers, and more complex operations. Without a proper system, errors increase, costs rise, and delays happen. This leads to frustrated customers and lost revenue.
Six Sigma helps businesses streamline their operations and reduce mistakes. By applying structured frameworks like DMAIC, SMEs can find the root causes of inefficiencies and fix them. This ensures smoother workflows and better resource management.
Avoiding Costly Technology Mistakes
Many SMEs invest in new technology without proper planning. They may adopt complicated software or digital tools that do not integrate well. These mistakes lead to wasted money and operational confusion.
By using Six Sigma, SMEs can ensure that technology decisions are data-driven and aligned with business needs. Instead of blindly adopting new systems, businesses can analyze whether a tool will truly improve efficiency.
"When technology fails too often it is because of human error." |
|| Read more: Common Technology Mistakes SMEs Make When Expanding
Applying Six Sigma in the Digital Age
Today, businesses are moving towards automation, AI, and digital solutions. While these technologies promise efficiency, they must be properly managed and optimized. Six Sigma ensures that digital transformation efforts are effective and sustainable.
Instead of relying only on automation tools, businesses should apply Six Sigma principles to track performance and identify problems. This ensures that digital processes work smoothly and deliver real results.
Combining AI with Six Sigma
AI and automation improve efficiency, but they also require continuous monitoring and improvement. Many businesses struggle with poor AI implementation, leading to *errors, misinterpretations, and inefficiencies.
Six Sigma provides a framework for testing and refining AI applications. It ensures that AI-driven decisions are accurate and beneficial. By applying Six Sigma methods, businesses can reduce AI-related risks and maximize performance.
Optimizing Automation and Workflows
Many businesses invest in automation tools but fail to achieve full efficiency. This happens when workflows are poorly designed or not optimized. Automation alone does not guarantee success—processes must be carefully structured.
With Six Sigma, businesses can analyze workflows, remove inefficiencies, and ensure that automation delivers true value. This leads to faster operations, fewer errors, and lower costs.
|| Read more: DeepSeek V3 vs. ChatGPT-4o – Is It Comparable?
Real-World Application: How Six Sigma Can Improve Your Business
Many companies across different industries have used Six Sigma to improve efficiency and reduce costs. This method helps businesses find and fix weaknesses in their processes, leading to better results.
For example, a logistics company that struggled with order fulfillment delays used Six Sigma to analyze its supply chain. By identifying key bottlenecks and optimizing warehouse operations, the company reduced shipping delays by 30% and improved order accuracy by 25%.
Six Sigma in Software Development
In the technology industry, software companies apply Six Sigma to improve product quality, reduce errors, and streamline development processes. By using data analysis, companies can detect and eliminate coding defects early, ensuring better software performance.
One software company reduced system crashes by 40% in six months by applying Six Sigma’s DMAIC framework. They focused on analyzing failure patterns, fixing bugs early, and improving testing procedures. This led to higher customer satisfaction and reduced maintenance costs.
Six Sigma in Logistics and Fulfillment
Businesses involved in shipping, warehousing, and order fulfillment rely on Six Sigma to optimize processes and improve accuracy. Companies that process thousands of orders daily need error-free workflows to avoid delays and extra costs.
One fulfillment center implemented Six Sigma to analyze its warehouse layout and picking process. After reorganizing storage zones and using automation, they reduced order processing time by 35% and cut labor costs by 20%.
|| Read more: What is an Elevator Pitch? Steps to Create an Elevator Pitch
Conclusion: Should Your Business Adopt Six Sigma?
Six Sigma is not just a method for large corporations—it is a powerful tool that businesses of all sizes can use to improve quality, reduce costs, and increase efficiency. Whether in manufacturing, logistics, technology, or service industries, companies that apply Six Sigma see faster workflows, fewer errors, and higher customer satisfaction.
For SMEs, adopting Six Sigma provides a structured way to scale while maintaining efficiency. Businesses that integrate Six Sigma with digital transformation, AI, and automation can achieve smoother operations and sustainable growth.
Key Takeaways
- Six Sigma helps businesses reduce errors, improve efficiency, and optimize processes.
- SMEs can use Six Sigma to scale effectively without losing quality.
- Applying Six Sigma in logistics, software, and automation leads to measurable cost savings.
- Integrating Six Sigma with AI and digital transformation ensures better data-driven decision-making.
- Companies that focus on continuous process improvement stay ahead of competitors.
Are you ready to improve your business efficiency? Start applying Six Sigma today and see the results in quality, cost savings, and productivity.